Vaccum Forming Services
low cost and efficient plastic production Process
- Low Tooling Investment
- Versatile and Cost Effective
- Rapid Prototyping Development
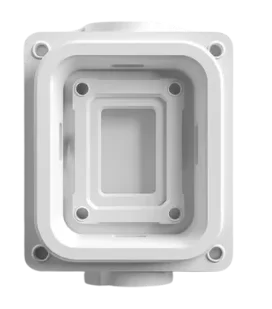
Looking for vacuum forming solutions to bring your product to market?
We are the partner you need
At OAK E&M, our advanced thermoforming techniques and dedicated team of experts ensure flawless execution at every stage. We’re committed to delivering custom manufacturing solutions that exceed expectations, helping you stay ahead in today’s competitive market. Let’s bring your vision to life
Let us help you choose the right machining service for your needs
Our team of experts and experience engineers are eager the help you reach your goals faster and more efficient.
Vacuum Formed Available Materials
Polystyrene
Key Properties:
- Lightweight and rigid
- Excellent impact resistance
- Good dimensional stability
- Cost-effective
Common Applications:
- Food packaging
- Disposable cutlery
- Electronics housings
- Point-of-purchase displays

Policarbonate
Key Properties:
- Exceptional impact strength
- High heat resistance
- Optical clarity
- UV resistant (with additional treatment)
Common Applications:
- Automotive components
- Medical device housings
- Safety shields and guards
- Lighting fixtures
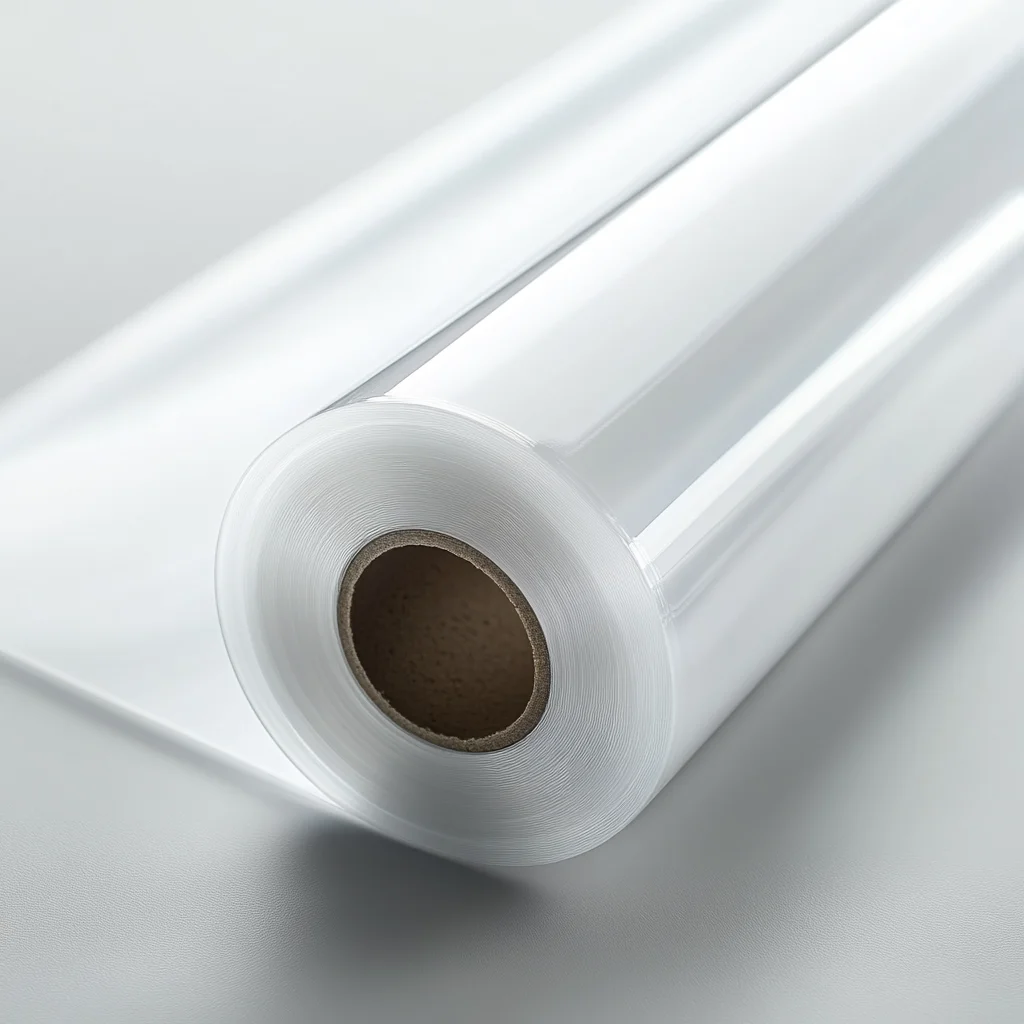
ABS
Key Properties:
- High impact resistance
- Good chemical resistance
- Excellent surface finish
- Easy to paint and glue
Common Applications:
- Automotive interior parts
- Consumer electronics casings
- Protective equipment
- Luggage and cases

Kydex
Key Properties:
- Excellent formability
- High impact resistance
- Fire-retardant grades available
- Good chemical resistance
Common Applications:
- Aircraft interior components
- Medical equipment housings
- Mass transit interiors
- Heavy equipment dashboards
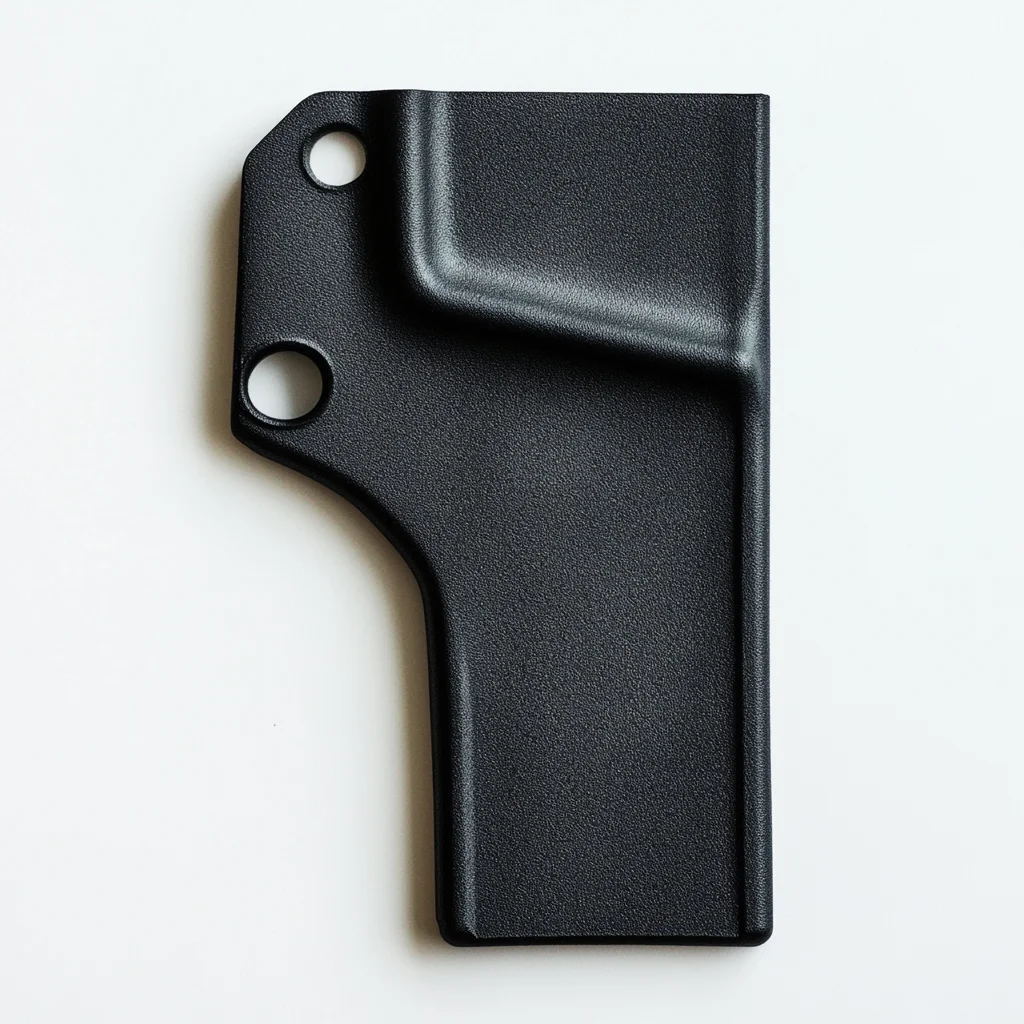
HDPE
Key Properties:
- Excellent chemical resistance
- Good impact strength
- Moisture resistant
- FDA compliant grades available
Common Applications:
- Chemical storage tanks
- Food processing equipment
- Outdoor furniture
- Playground equipment
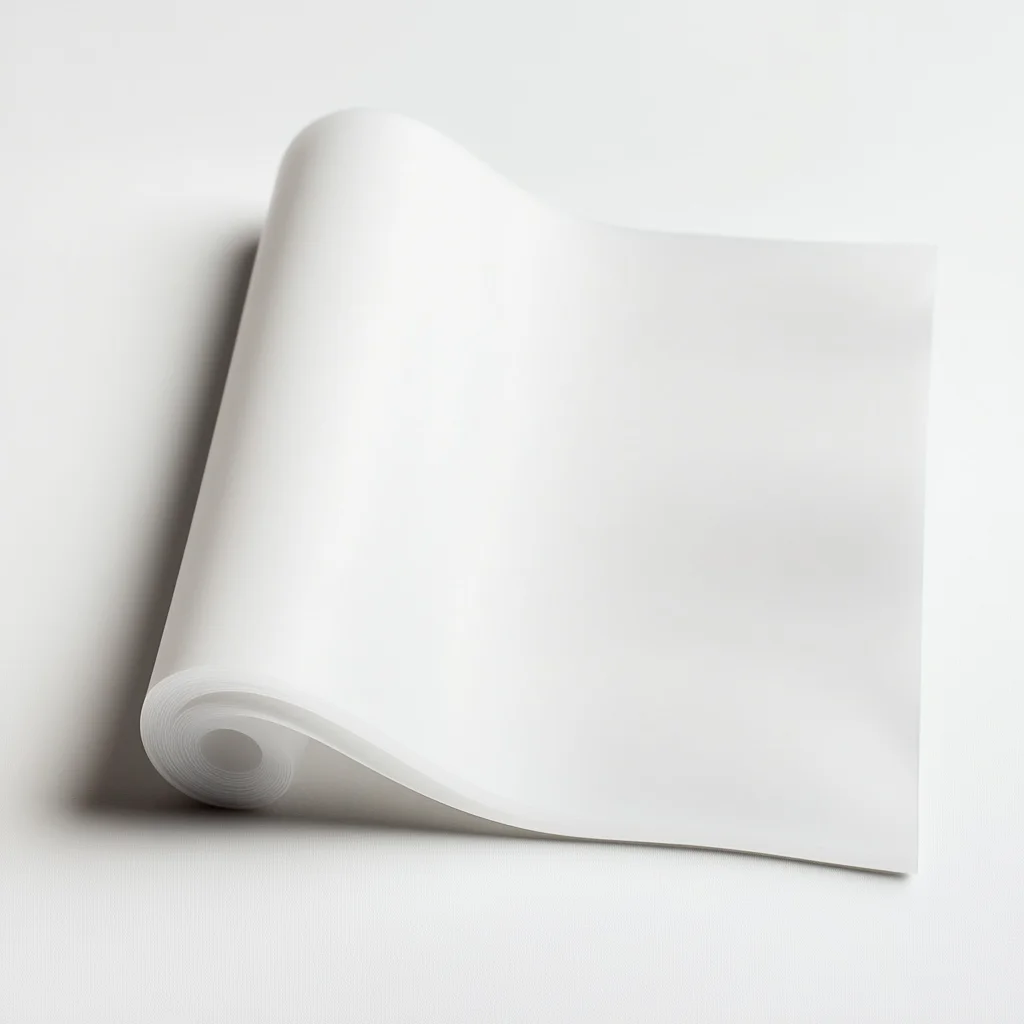
TPO
Key Properties:
- Excellent weather resistance
- Good chemical resistance
- Low density
- Recyclable
Common Applications:
- Automotive bumpers and trim
- Roofing membranes
- Outdoor signage
- Industrial floor mats
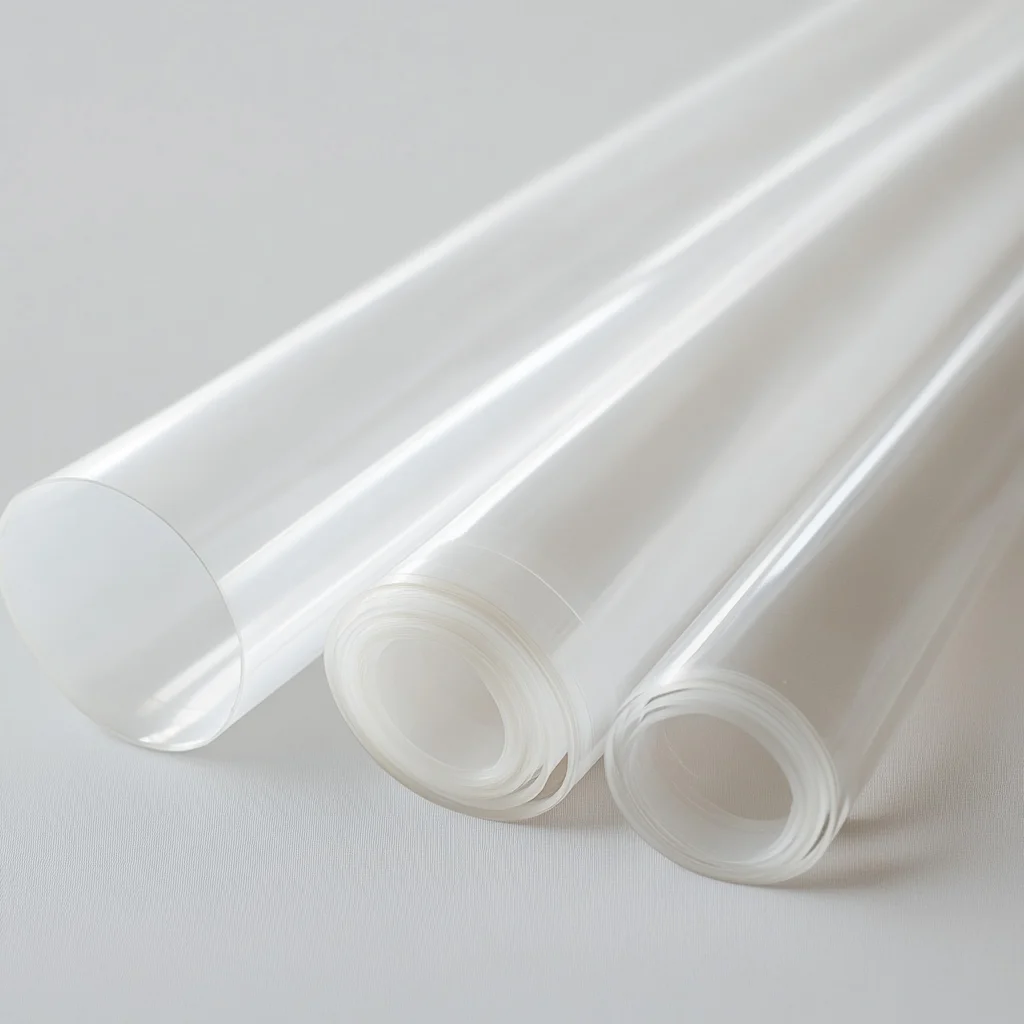
PVC
Key Properties:
- Flame retardant
- Chemical resistant
- Durable and long-lasting
- Available in various grades (rigid and flexible)
Common Applications:
- Construction materials
- Electrical conduit and fittings
- Medical tubing
- Automotive interior tri
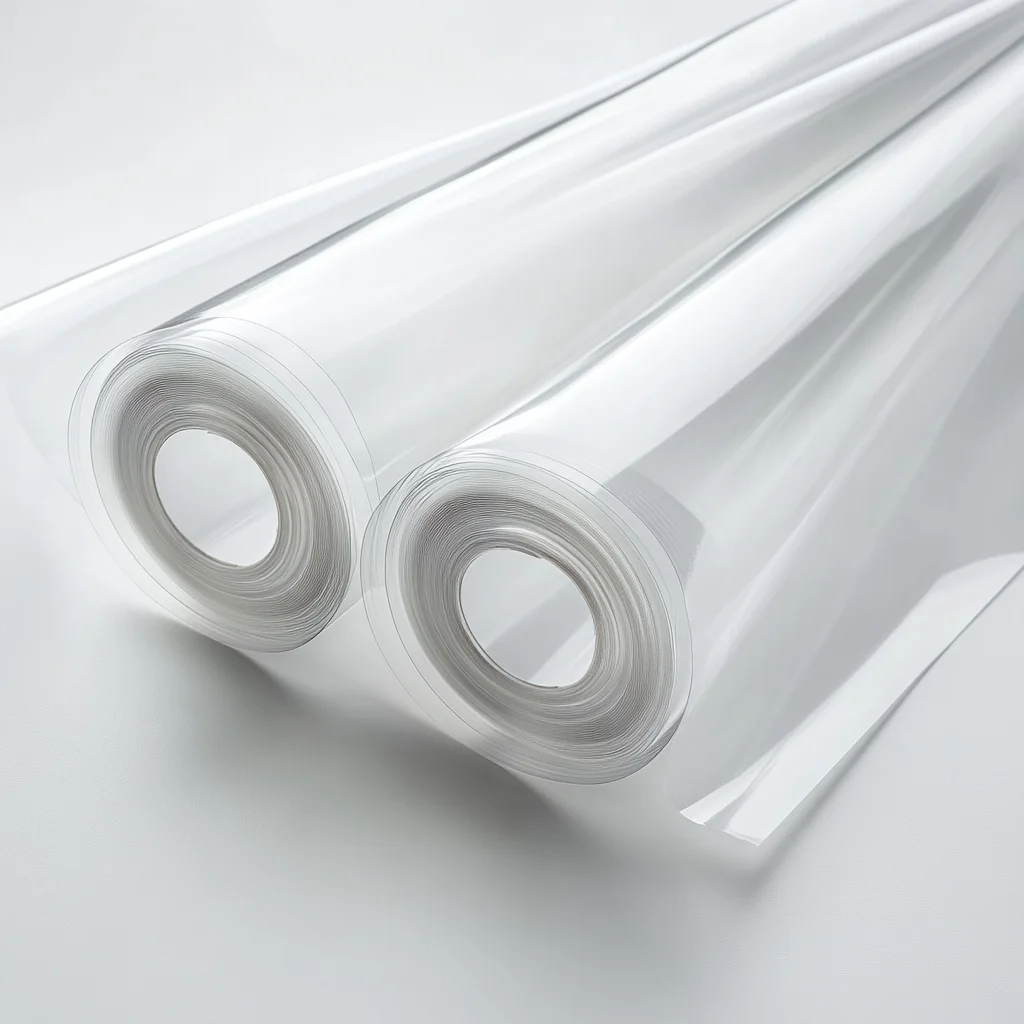
Vacuum Forming Machine Tolerance
Your one-stop solution for high-quality, custom thermoformed components
Maximum Part Size
X: 48 Inches (1,219mm) | Y: 24 Inches (610 mm)
Thickness
1/16″ – 1/4″
Available Colors
Variety of colors depending on the type of material. We can confirm on quotation.
Threads and Tapped Holes
We can accommodate any standard thread size. We can also machine custom threads; these will require a manual quote review.
Surface Finish
The standard finish is as-machined: 125 Ra or better. Additional finishing options can be specified when getting a quote.
Standard Lead Time
3 – 5 Business Days
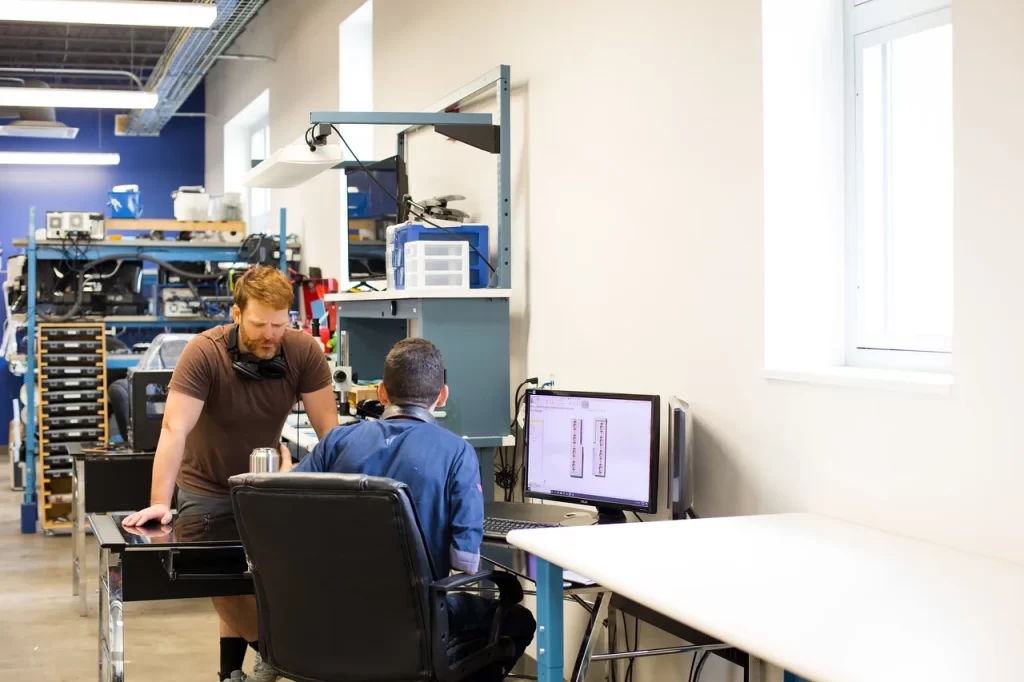
Need Help Getting Your Parts Just Right?
Our team of first-hand engineers are committed to your part’s perfection.
Engineers dedicated to your project’s success, providing hands-on assistance and expert advice to ensure your custom parts are perfect from start to finish.
Discover the benefits of partnering with us
First-hand Experienced Engineers
Our team, composed of engineers who have been clients themselves, understands the challenges of prototyping and manufacturing. This experience enables us to offer personalized service and solutions that meet our clients' specific needs.
Reliability and Precision Everytime
Our commitment to unmatched precision and reliability builds trust with our clients. You can count on us to turn their ideas into reality, exactly as they envision, especially in sectors like aerospace where precision is crucial.
Advanced Technological Integration
OAK E&M leverages cutting-edge technology to enhance the precision of our products and enable complex designs that traditional methods can't achieve.
Customized Solutions
We excel at providing customized solutions tailored to each project's specific needs. Our ability to adapt and create unique solutions not only meets client expectations but also distinguishes us from competitors who only deliver the part or prototype you ask.
Rapid Project Execution
Our commitment to efficiency means we complete projects with high precision and speed. This quick execution is crucial for clients with tight deadlines, giving them a competitive edge in fast-paced markets.
Proactive Problem Solving
Our team's proactive approach helps us address potential issues before they become problems. This foresight smooths out project flow, reduces downtime, and leads to higher client satisfaction thanks to our attention to detail.
Our team of experts engineers are ready to help you
Get Your Custom Quote in 24 Hours
Reviewed by a real-life experienced engineers
Enter details, upload your file and specify your needs.
Get a custom quote in 24 hours.
Ideal for large orders or orders with special needs.
Contact an Engineer
Our Team of Engineers are ready to help you
Need a one-on-one engineer support to get your part just right before manufacturing.
Contact Us Now!
Our Process is what makes the difference
01
Understanding your projects
We start by thoroughly understanding your project’s requirements, ensuring we capture every detail to deliver the perfect part tailored to your specific needs.
02
Ensuring Manufacturability
We will review your designs thoroughly, ensuring every custom part is manufacturable, optimizing efficiency, and minimizing costly errors.
03
Part production plan and timeline
We create a detailed production plan and timeline, outlining each step to ensure efficient, timely, and precise manufacturing of your custom parts.
04
Final part
production
We proceed with the final production, followed by careful packaging to ensure your parts arrive in perfect condition, ready for immediate use.
Why Vacuum Forming is a Great Option For You?
Vacuum thermoforming offers a powerful combination of versatility, cost-effectiveness, and low initial investment. This manufacturing process excels at creating custom-designed parts with exacting detail and uniform quality. Compared to other production methods for plastic, metal, and FRP/fiberglass, vacuum forming presents several distinct advantages.
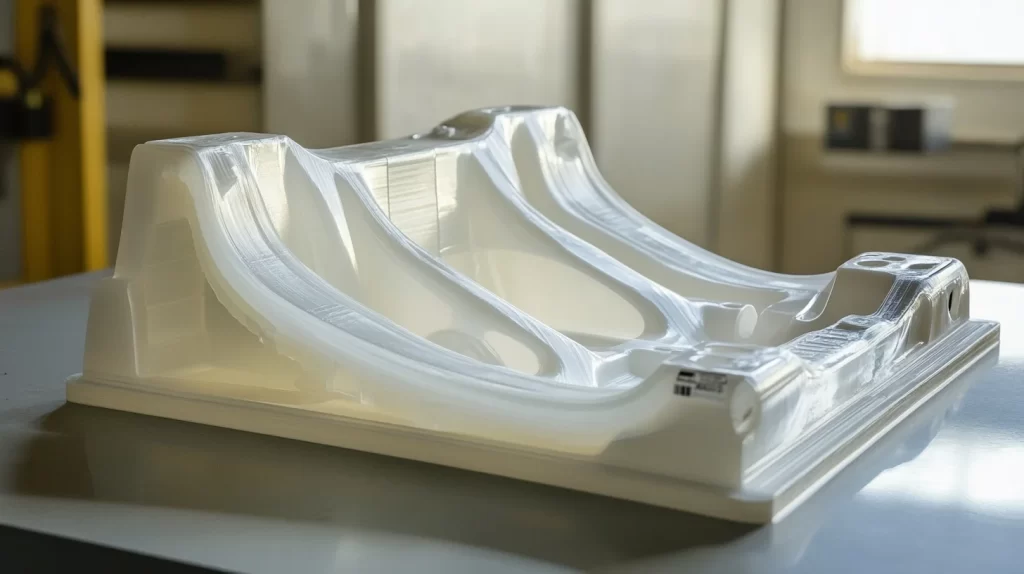
How Vacuum Forming Boosts Your Product Development?
Large Part Capability
At Low Cost
Create functional prototypes quickly, allowing for faster design iterations and reduced time-to-market.
Lightweight material
benefits
Achieve tight tolerances and highly repeatable results, ensuring quality across production runs.
Rugged and industry compliant
material performance
Work with a wide range of materials, from metals to plastics, to suit your specific product requirements.
Multi-part assemblies
and projects
Produce intricate designs and shapes that may be impossible with traditional manufacturing methods.
Low tooling
investment
Ideal for both prototypes and small production runs without the need for expensive tooling.
Rapid product
development
Easily scale from prototypes to full production as your product evolves.
FAQ
Our team is ready to help you with any question
What is vacuum forming?
Vacuum forming is a manufacturing process where a heated plastic sheet is stretched over a mold and then vacuum-sealed to create a precise shape.
What materials can be used in vacuum forming?
Common materials include various thermoplastics such as ABS, PETG, HDPE, polycarbonate, and PVC. The choice depends on the specific requirements of your project.
What are the advantages of vacuum forming over other manufacturing methods?
Vacuum forming offers lower tooling costs, faster production times, design flexibility, and the ability to produce both small and large parts cost-effectively.
What industries commonly use vacuum formed parts?
Vacuum forming is used in numerous industries including automotive, aerospace, medical, packaging, signage, and consumer products.
Can vacuum forming produce textured or detailed surfaces?
Yes, vacuum forming can reproduce intricate details and textures from the mold, allowing for a wide range of surface finishes and designs.
What is the typical turnaround time for a vacuum forming project?
Turnaround times can vary based on project complexity and volume. Generally, we can complete most projects within 2-4 weeks from design approval.
Starting a project and need helping getting your part just right?
Let’s talk, we are ready to help you get the perfect part.
Call Us: 352-448-8842